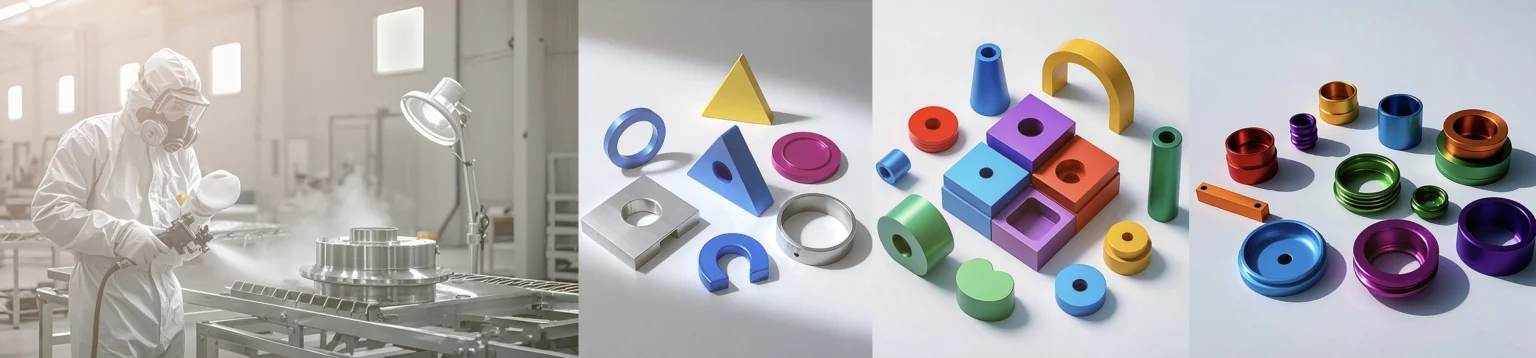
What is Heat Treatment ?
A series of operations in which solid steel products, either entirely or partially, are exposed to thermal cycles, causing changes in their properties and microstructure (JIS G 0201 Iron and Steel Terminology).
Heat Treatment of Steel
<Did You Know?>
Pure iron undergoes sudden changes in properties at 910°C. This temperature is called the A3 point. Below the A3 point, it is α-iron; above the A3 point, it is called γ-iron, where a crystalline transformation occurs. γ-iron transforms into δ-iron at 1390°C and melts at 1543°C. The state where iron is solid-solved with other elements is called ferrite. In the Fe-C system, ferrite can solid-solve up to 0.035% carbon. γ-iron is called austenite, which can solid-solve more carbon. At 1130°C, it solid-solves 1.98% carbon. At this point, carbon atoms invade the crystal lattice of γ-iron, forming an interstitial alloy. When austenite is slowly cooled, γ-iron transforms into α-iron and Fe3 (eutectoid transformation) at 723°C, producing pearlite.
Name | Target Material | Characteristics |
---|---|---|
Annealing (Toughening) | - | ※ Heat the metal to an appropriate temperature, maintain it at that temperature for a certain period, and then cool it gradually. When referring to annealing alone, it usually means full annealing. ※ Full Annealing: To completely eliminate the effects of cold working or quenching, heat evenly to the austenite-level temperature and then cool gradually. |
Normalizing | - | To eliminate deformation and coarse microstructure caused by room-temperature processing or rapid cooling, restore the normal structure by heating above the A3 point to achieve a uniform austenite phase, and then cool in still air. |
Quenching | - | ※ When γ-state steel is rapidly cooled, the diffusion of carbon does not occur, preventing the pearlite transformation. Instead, a lattice transformation occurs near room temperature, resulting in a high-hardness martensitic structure. Quenching refers to this entire process. Care must be taken during rapid quenching to avoid cracking. ※ Perform quenching and tempering in groups |
Tempering | - | ※ Quenched materials remain relatively brittle and are difficult to use for general purposes. Therefore, reheating the quenched steel at low temperatures (220–650°C) to restore the required toughness is called tempering. ※ Perform quenching and tempering in groups |
High-Frequency Quenching | Medium Carbon Steel C 0.3–0.5% | This method involves rapidly heating the surface of the steel using high-frequency induced current and then rapidly cooling it to achieve hardening. |
Carburizing Quenching | Low Carbon Steel C<0.3% | ※ This method involves heating low carbon steel in a carburizing material to allow carbon to penetrate the steel surface, increasing the carbon concentration near the surface. ※ While the surface becomes hardened, the interior remains low-carbon and unhardened, thus retaining high toughness. |
Nitriding Quenching | Nitriding steel SACM645 etc. | This method involves penetrating nitrogen into the steel surface to achieve surface hardening. |
Diffusion Nitriding® (Salt Bath Nitriding) | Steel | ※ To improve other properties, nitriding is referred to as soft nitriding. It is equally applicable to carbon steel and cast iron, enhancing wear resistance and fatigue strength. ※ Diffusion Nitriding® is a registered trademark of Durferrit GmbH (Germany). |
What is Surface Treatment?
To improve the corrosion resistance and surface appearance of materials, electroplating and coating are applied.
Category | Name | Target Material | Characteristics |
---|---|---|---|
Chemical Treatment(Chemical Coating) | Trivalent Chromate Treatment | Steel | After galvanizing, immerse it in a chromic acid solution for a few seconds to form a chromate film. Although this film is extremely thin, it protects the galvanized layer and effectively prevents the formation of white corrosion products when exposed to external air. It does not contain hexavalent chromium, a harmful substance specified by RoHS. |
Chemical Treatment(Chemical Coating) | Ferric Oxide Coating (Blackening) | Steel Bolts, Nuts, Measuring Instruments | Immerse iron in an aqueous NaOH solution and boil it to form a black Fe3O4 film on the surface. The black coating is uniform, approximately 1–2μm thick, porous, and non-electrically insulating. It is not recommended for parts requiring high rust resistance. |
Electroless Plating | Electroless Nickel Plating | Steel, Stainless Steel, Copper, Aluminum Alloy, Glass, Plastic | No electricity is used; the plating solution contains a reducing agent with electrical effects. With proper pre-treatment, it can plate all objects. Although the film thickness is uniform, the plating speed is relatively slow. |
Anodizing Treatment | Acid-Resistant Aluminum | Light Metals Such as Aluminum and Titanium | The material in the electrolyte is set as the anode for electrolysis, producing a thick oxide film on the anode. It offers wear resistance, corrosion resistance, electrical insulation, and heat resistance. Depending on the material and electrolyte, the color of the film may change, allowing for possible dyeing. |
Appearance Colors of Surface Treatments
Trivalent Chromate | Electroless Nickel Plating | Ferric Oxide Coating | Acid-Resistant Aluminum (White) | Acid-Resistant Aluminum (Black) |
![]() | ![]() | ![]() | ![]() | ![]() |
Thank you for reading. We hope this article has been helpful to you. Of course, you are also welcome to contact us via email or instant chat. We are more than happy to assist you in solving your problems.